
Unlike humans, cobots perform the same task the same way, every time, without growing tired or suffering any loss in performance. This includes welding small pieces together, drilling screws, and similar assembly tasks.Ĭobots can also be used to assist with quality assurance during the production process. Universal Robots’ cobots are specifically designed to work alongside human employees and relieve them from tedious and difficult assembly jobs. Meanwhile, machine tending tasks, including those that involve heavy duty CNC machines, are also within the capabilities of Universal Robots’ cobots. Heavy materials can easily be lifted and transported across factory floors using mobile robot platforms. Industries that use robots in manufacturing see significantly fewer workplace injuries. Additionally, many material handling tasks are repetitive, which can give rise to repetitive strain injury. Materials such as metal, plastic and other substances can pose a great risk to human workers. Material handling is one of the most dangerous jobs in manufacturing. Below, we summarize three common classes of cobot deployments. These include assembly, dispensing, finishing, machine tending, material handling, welding, material removal, quality inspections, and more. There are many collaborative robot applications across all industries. By contrast, cobots are compact and flexible and can operate without safety cages or fencing directly alongside people. Traditional industrial robots are often mammoth-sized machines that are also static and difficult to repurpose and reprogram. Robots are able to improve the efficiency and safety of many industries by assuming dull, dirty and dangerous jobs. Even though there are many ways to implement robotic technology, the goals of such machines are similar across all industries and processes-improved production. There are a wide variety of industrial robot applications. Read on to learn more about the capabilities of industrial robots in general and then we’ll look at some recent, innovative cobot applications. From personal protective equipment manufacturing to swab testing, cobots are improving the efficiency, safety, and quality of countless processes. With the world battling Covid-19, 2020 delivered some ingenious cobot implementations. The vast majority of cobot implementations are found in manufacturing and industrial environments, but cobots have the flexibility to be used in a wide variety of sectors from agriculture and medical to pharma. Cobots are more flexible than standard or traditional industrial robots, which means that they can be deployed on a wide variety of tasks from machine tending and welding to packaging & palletizing.
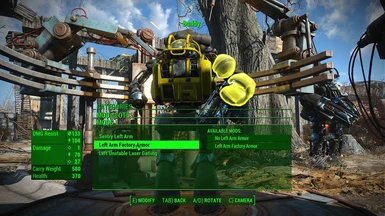
Cobots are low cost industrial robots that are safe to operate in close proximity to humans. Industrial robot applications have seen massive growth over the last decade, as a variety of industries have realized the potential of industrial robots and, more importantly, collaborative robot (or ‘cobots.’).
